Here to help every business grow
Across a range of sectors we’re boosting productivity, saving time and increasing revenue. Don’t believe us? Explore our customer success stories below.
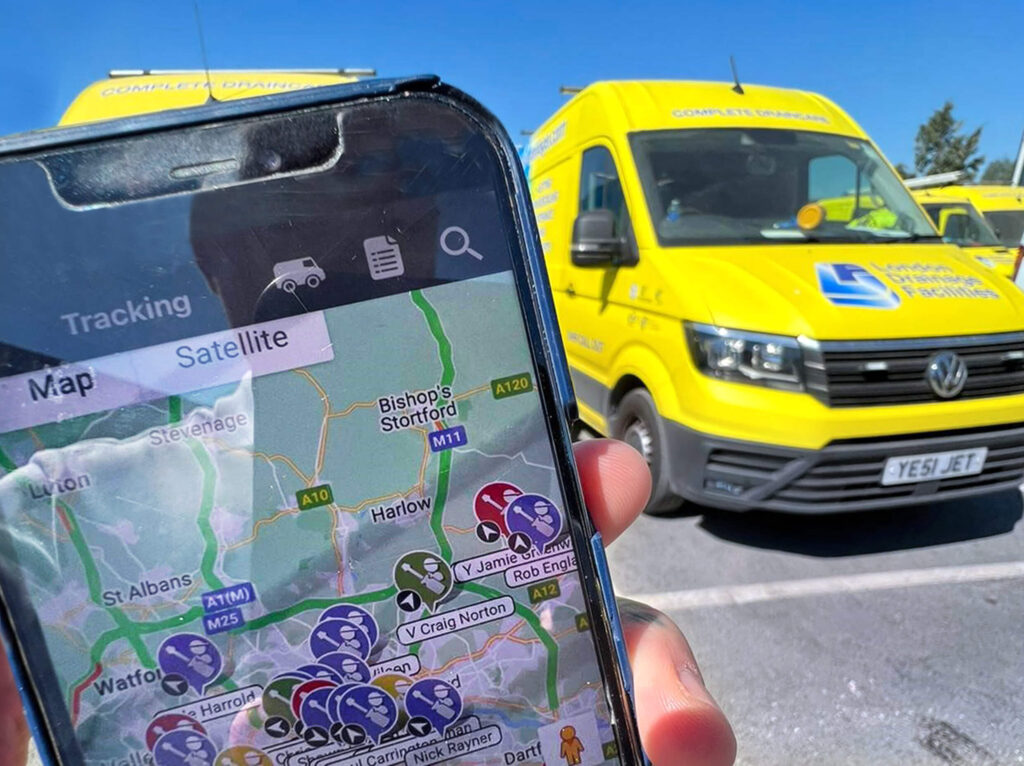
Drainage, waste and environmental
London Drainage Facilities Boosts Business Growth with BigChange Mobile Tech.
London Drainage Facilities (LDF) is achieving 15 percent annual growth following the introduction of a job management system from BigChange.
Thank you! Your submission has been received!
Oops! Something went wrong while submitting the form.
No results found